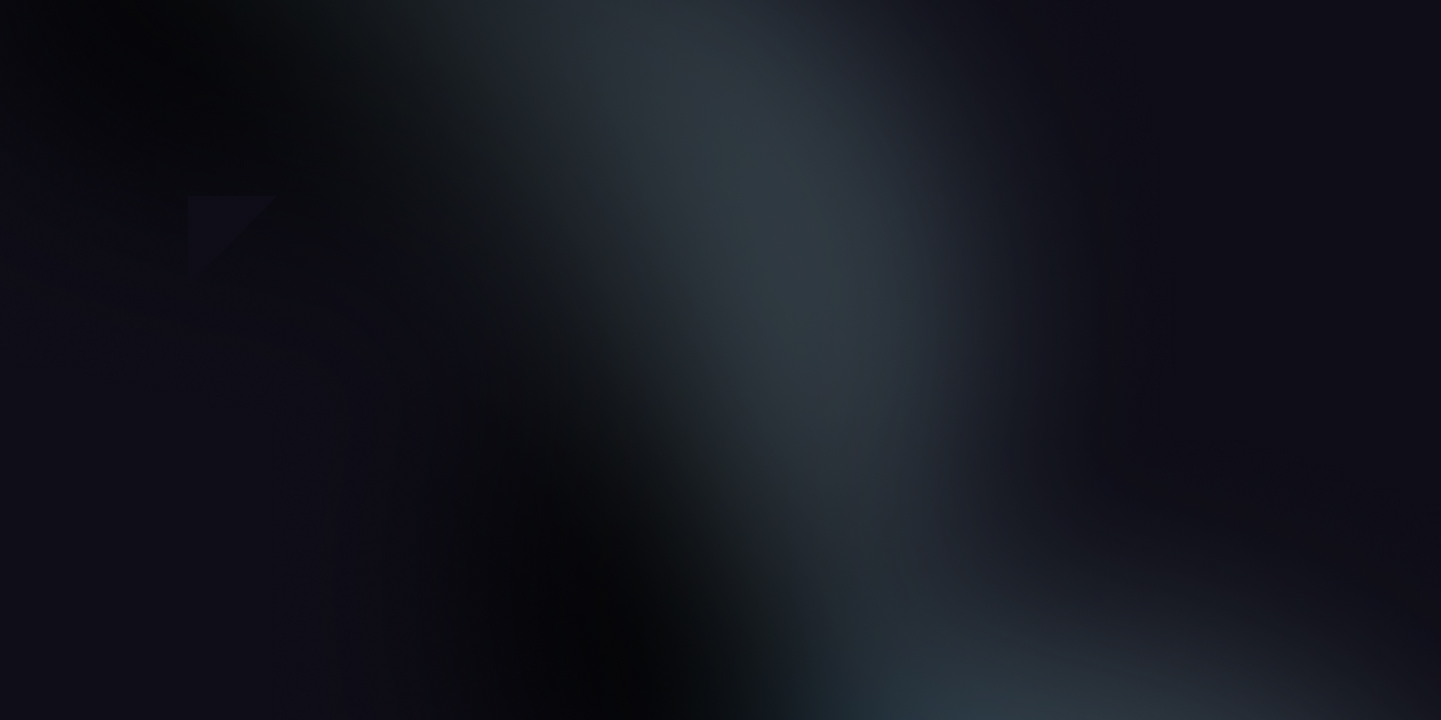
How to choose a circular saw blade
Publié le 17 May 2024
Choosing the right circular saw blade depends on the material you're going to cut, the type of cut you want to make and the specifications of your machine.
You should choose the smallest blade diameter close to your needs for maximum rigidity. The thickness must be adapted to the diameter. The choice of teeth depends on the material to be cut, its cross-section, cutting depth and cutting parameters. The circular saw blade can be equipped with a keyway or drive holes.
Define the characteristics of your circular saw blade
Choosing the right circular saw blade is essential to guarantee precise, efficient cuts. There are several factors to consider when selecting the right blade for your needs.
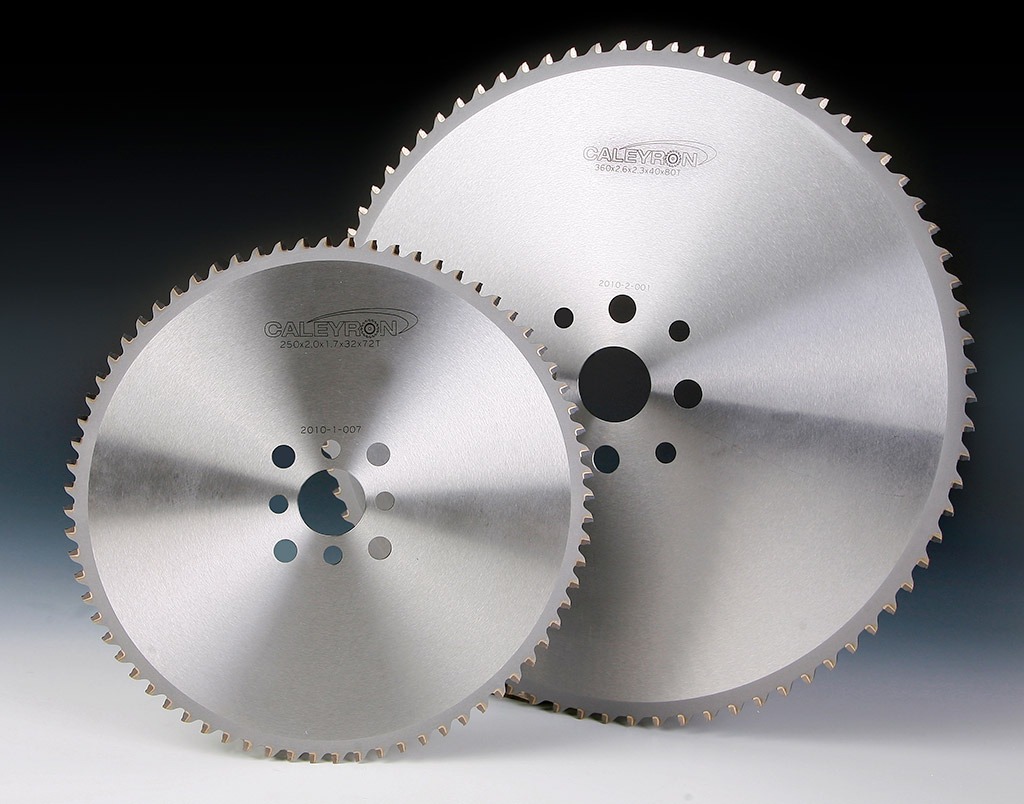
1. Blade types :
The type of blade depends on the application: HSS or HSS-E saw blades, solid carbide saw blades, carbide-tipped saw blades.
2. Applications :
Circular saw blades are designed to cut different types of material such as metal, copper, bronze, aluminum, plastic... Make sure you choose the right blade for the material you're going to cut.
3. Blade dimensions :
Define the required blade dimensions, including diameter, thickness, bore, to ensure correct fit and compatibility with your cutting machine or process for optimum performance.
- Diameter: determine the smallest possible diameter that is compatible with your machine to maximize rigidity and minimize vibration.
- Thickness: must be proportional to diameter to ensure stability and cutting precision.
- Bore: the blade bore must match the machine spindle for secure mounting.
4. Machine :
The choice of machine is also important. It must be rigid, with the best possible workpiece clamping system.
5. Toothing: (Z) (relative to the material to be cut, its cross-section and cutting depth)
The choice of teeth is decisive in obtaining the best possible cut.
- The number of teeth: there is a fine or coarse tooth set according to the DIN standard, which corresponds to the standard dimensions, or it is possible to determine a tailor-made (non-standard) number of teeth.
- La géométrie de la dent: la forme A (DIN 1837) correspond à la denture fine tandis que la forme B (DIN 1838) correspond à la denture grosse. Les dents peuvent également être chanfreinées :
- AW, BW, teeth are chamfered one tooth to the left and the next to the right.
- C, the upper tooth is chamfered on both sides and the lower tooth is unchamfered.
- BR, with chip breaker.
Chamfers are used to break up the chip.
Cutting and clearance angles are determined according to the material to be machined.
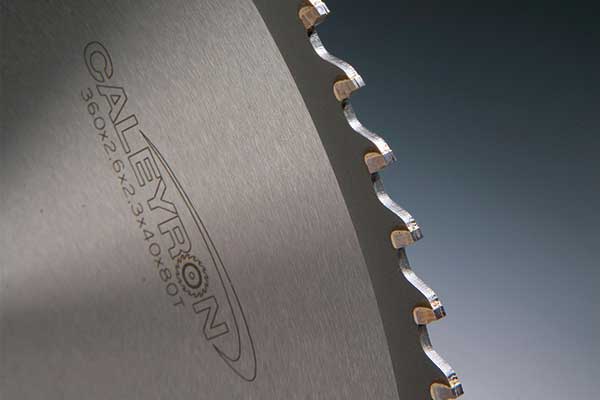
6. Blade coating and surface treatment :
The coating of a milling cutter plays a crucial role in its efficiency and durability. Depending on the type of material to be machined and the desired requirements, the coating is a decisive factor. Here are some of the main functions of a milling cutter coating:
- Wear resistance
- Reduced friction
- Resistance to thermal stress
- Corrosion prevention
- Reduced residue build-up
- Improved lubrication
- Avoid overheating
- Optimum grip
Circular saw blade reminder
Circular saw blades are essential for cutting and sawing. They are mainly made from HSS high-speed steel, solid carbide and carbide inserts. HSS blades are highly efficient on most steels. Solid carbide blades offer superior durability and excellent cutting performance on hard materials. Carbide also permits higher cutting conditions.
It's worth remembering that the first thing to do before buying a circular saw blade is to determine your cutting objective. Then, by taking into account the characteristics presented above, you can choose the circular saw blade that best suits your needs, in order to obtain the best performance.
If you have any questions or need advice about your circular saw blades, don' t hesitate to contact us!