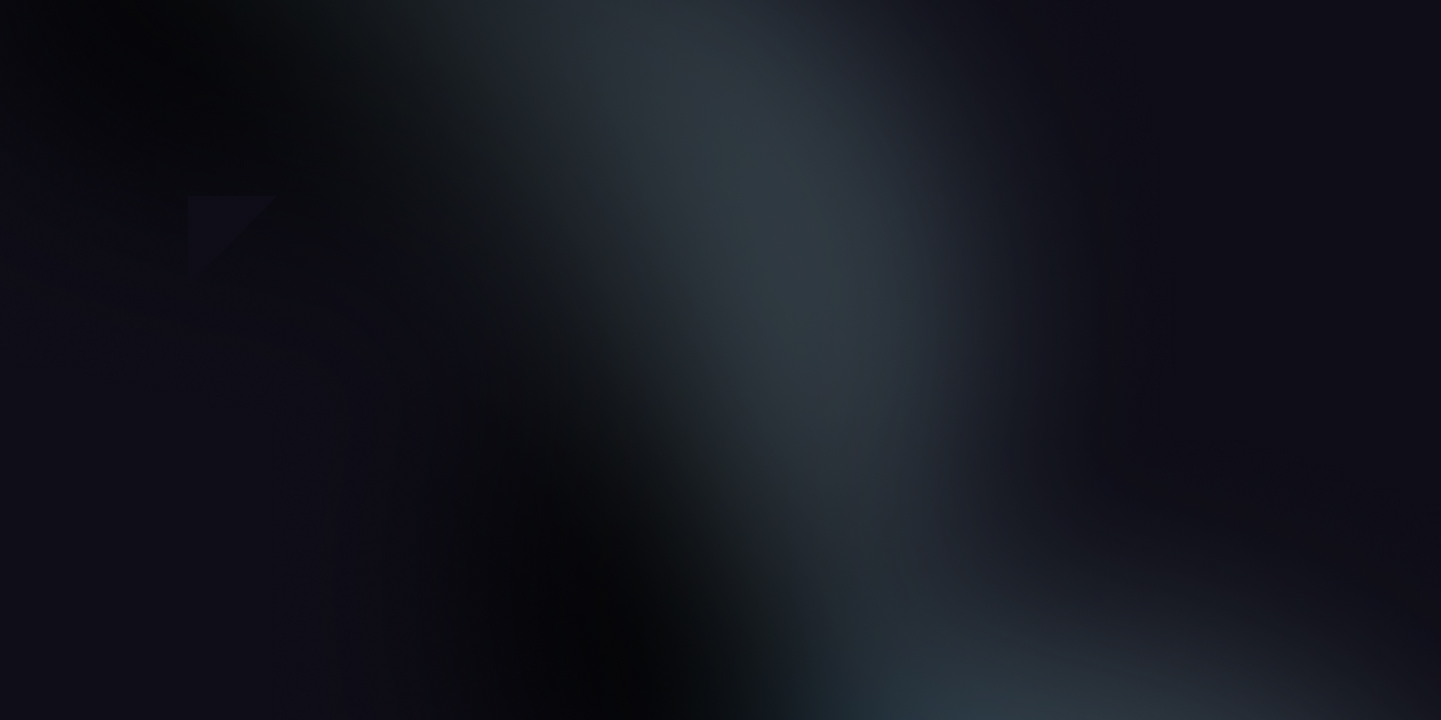
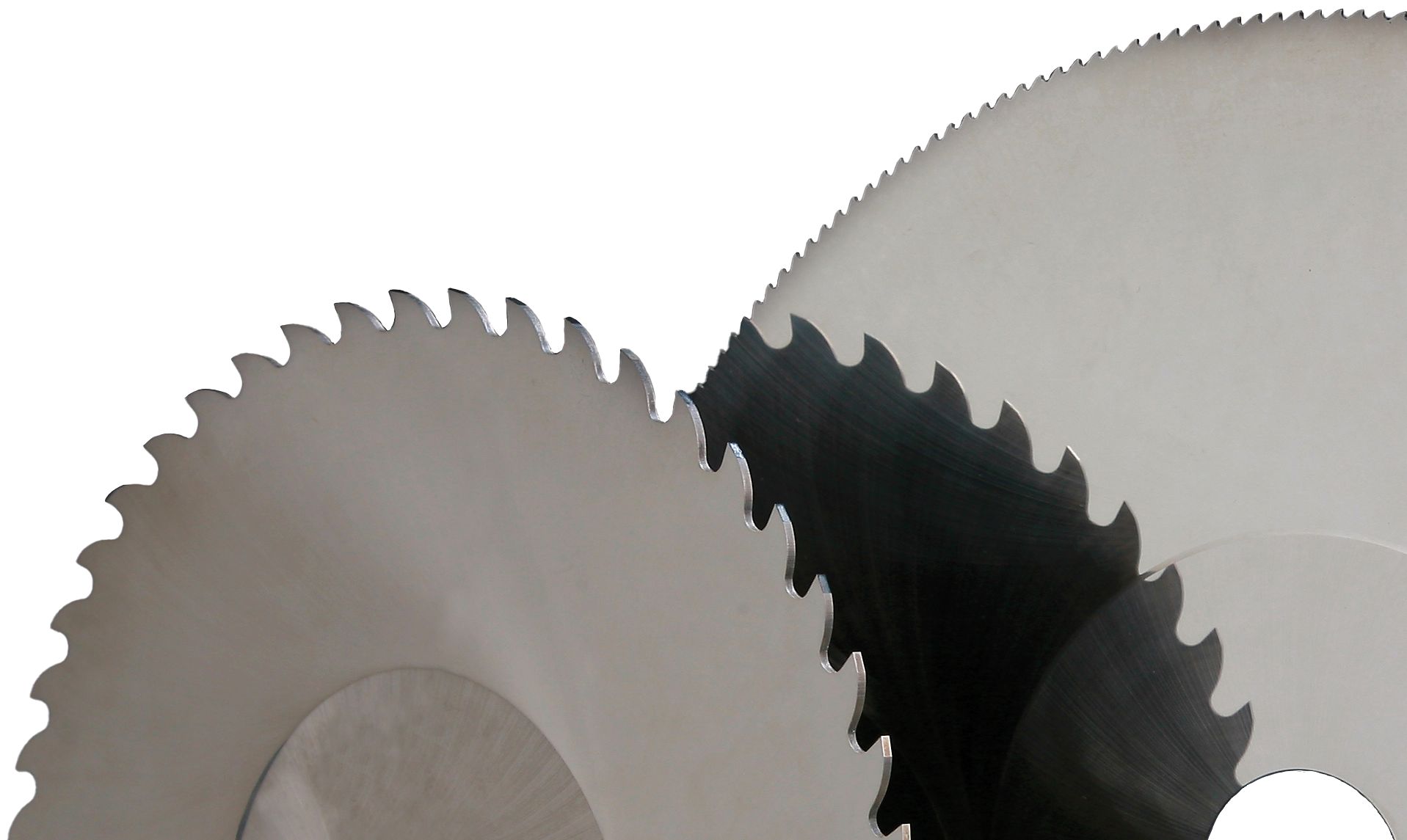
Coatings and surface treatments
Coatings and surface treatments on circular saw blades and circular knives are essential for improving the performance and quality of cutting tools.
Performance, durability and quality : the coating makes the difference
Each coating is selected according to the specific requirements of the application and the material to be machined.
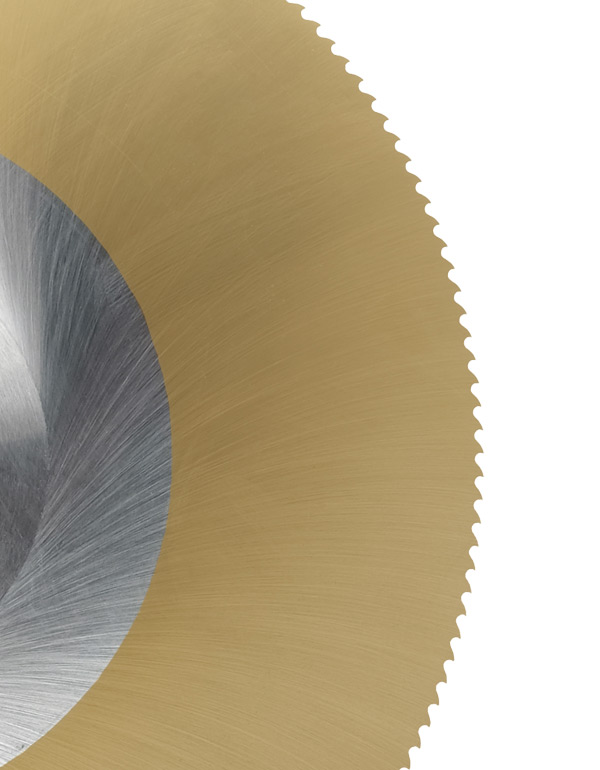
The benefits of surface coating
Increased tool life
Reduced tool changes, machine downtime and tool inventories.
Quality improvement
- Improved surface quality
- Compliance with dimensional tolerances
- Reduced production scrap
Productivity improvement
- Optimized cutting conditions
- High-speed machining possible
- Dry machining for certain applications
- Reduced heat build-up and material adhesion to the tool
Solution | Material | Coating | Advantages |
---|---|---|---|
GOLD | Steel | TiN | Versatile, wear-resistant, reduces abrasion and adhesive wear in various applications |
PERFORM | Steel | AlCrN | • Superior wear resistance and increased hardness • Enhanced performance with improved toughness Better coating adhesion due to reduced internal compressive stresses • Reduced crater wear on HSS tools due to lower thermal conductivity • More resharpening cycles per tool |
VOLCAN | Stainless Steel | TiAlN | • Suitable for tough conditions • Highly resistant to crater wear and oxidation • Ideal for both lubricated and dry machining |
COBRA | Titanium | AlTiSiN | • Revolutionary smooth coating, no post-treatment (polishing) required • Exceptional wear and oxidation resistance • Resists thermal stress • Superior results in hard machining • Maximum tool precision |
SUPRA | Cast Iron | AlCrN | • Optimal layer adhesion • High stability under thermal shocks • Perfect for heavily stressed cutting edges |
RAINBOW | Copper / Brass / Bronze / Silica-charged Aluminum (6 to 12%) | ta-C | • Ultra-thin coating maintains sharp cutting edges • Superior smoothness prevents material adhesion • Extreme hardness for increased wear resistance |
Frequently Asked Questions
What types of coatings are available and in what situations are they used ?
We offer several types of coatings, including Titanium Nitride (TiN), Titanium Carbonitride (TiCN), Titanium Aluminum Nitride (TiAlN), Chromium Nitride (CrN), and Chromium Aluminum Nitride (AlCrN). Each coating is tailored to specific materials and machining conditions.
How do surface coatings improve the quality of machined parts ?
Surface coatings help achieve smoother surface finishes, maintain the required dimensional tolerances, and reduce scrap production by enhancing tool performance.
How do surface coatings contribute to improving the quality of machined parts ?
Each coating type offers specific benefits. For example, TiN is ideal for machining steels, while CrN is effective for machining copper, brass, and titanium. The choice of coating depends on the material being machined and cutting conditions.
How to choose the right coating for a specific application ?
The choice of coating depends on various factors, including the material to be machined, cutting conditions, cutting speed, and quality requirements. Our experts can help you select the most suitable coating for your specific needs.
What criteria should be considered when evaluating the performance of surface coatings?
The performance of surface coatings can be evaluated based on their durability, wear resistance, thermal and chemical stability, and their ability to enhance productivity and the quality of machined parts.
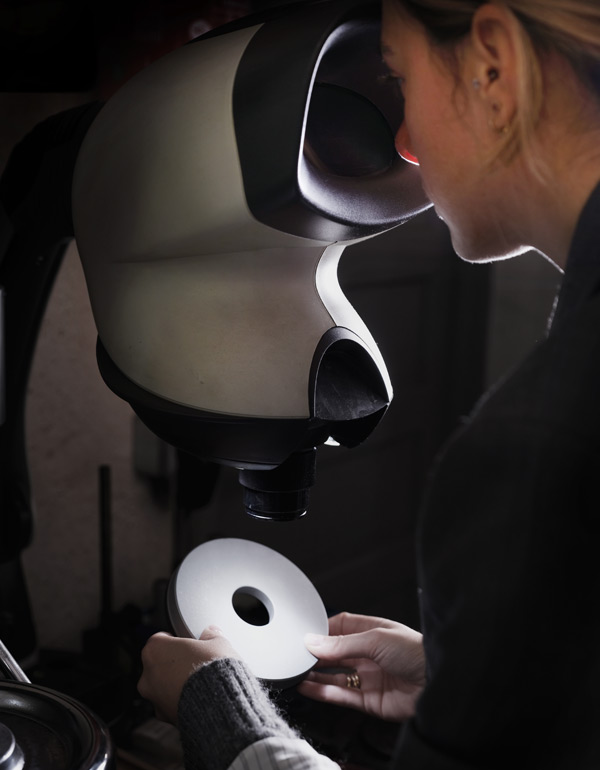
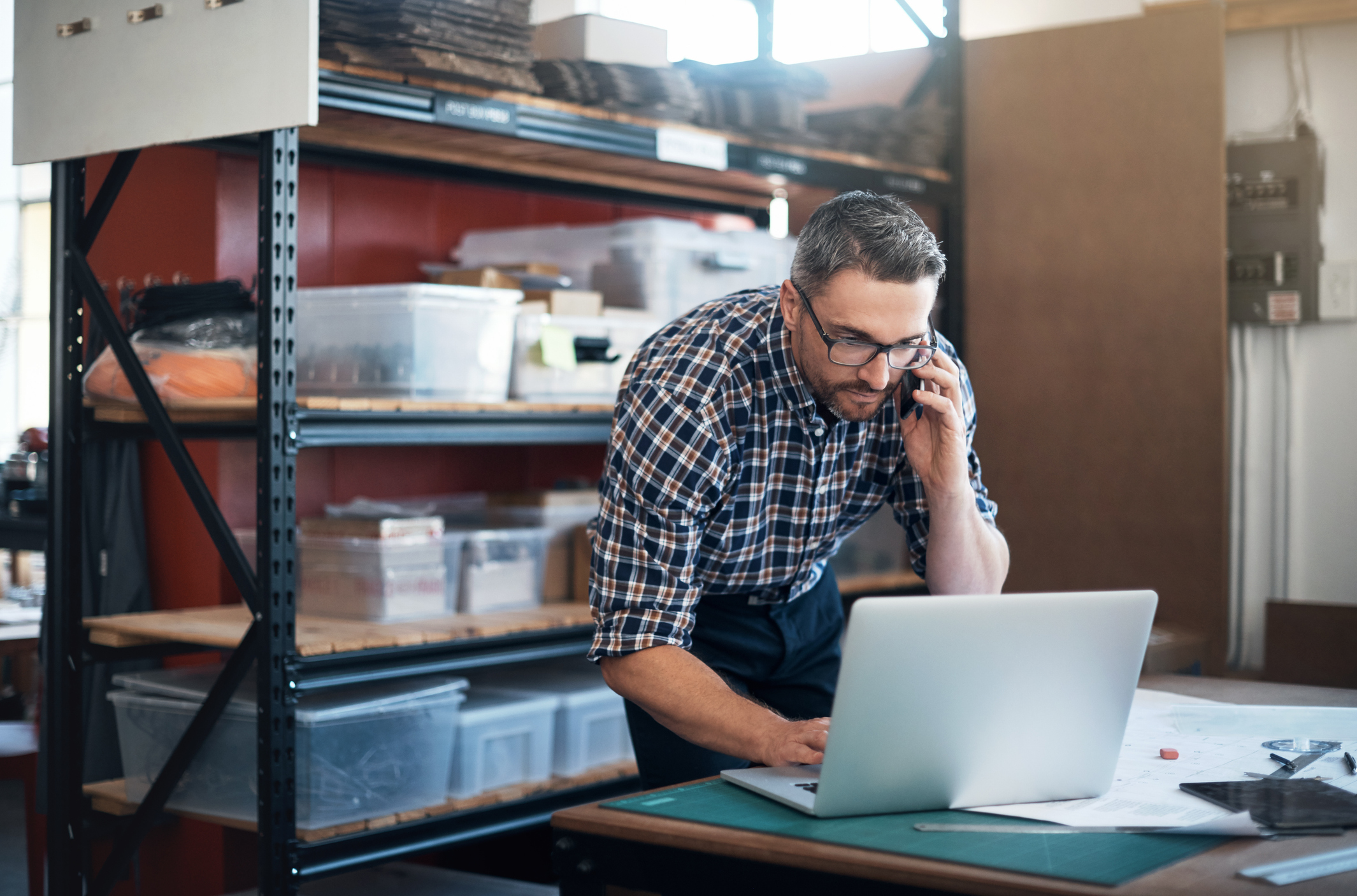
Do you need reliable, long-lasting
cutting tools?
Advice on the type of blade to use, the ideal coating…
our experts are here to listen and advise you